Supply chain vs procurement: Understanding the differences and importance of each
Wondering what the differences are between supply chain vs procurement? Learn how these functions are related, and best practices for integrating them.
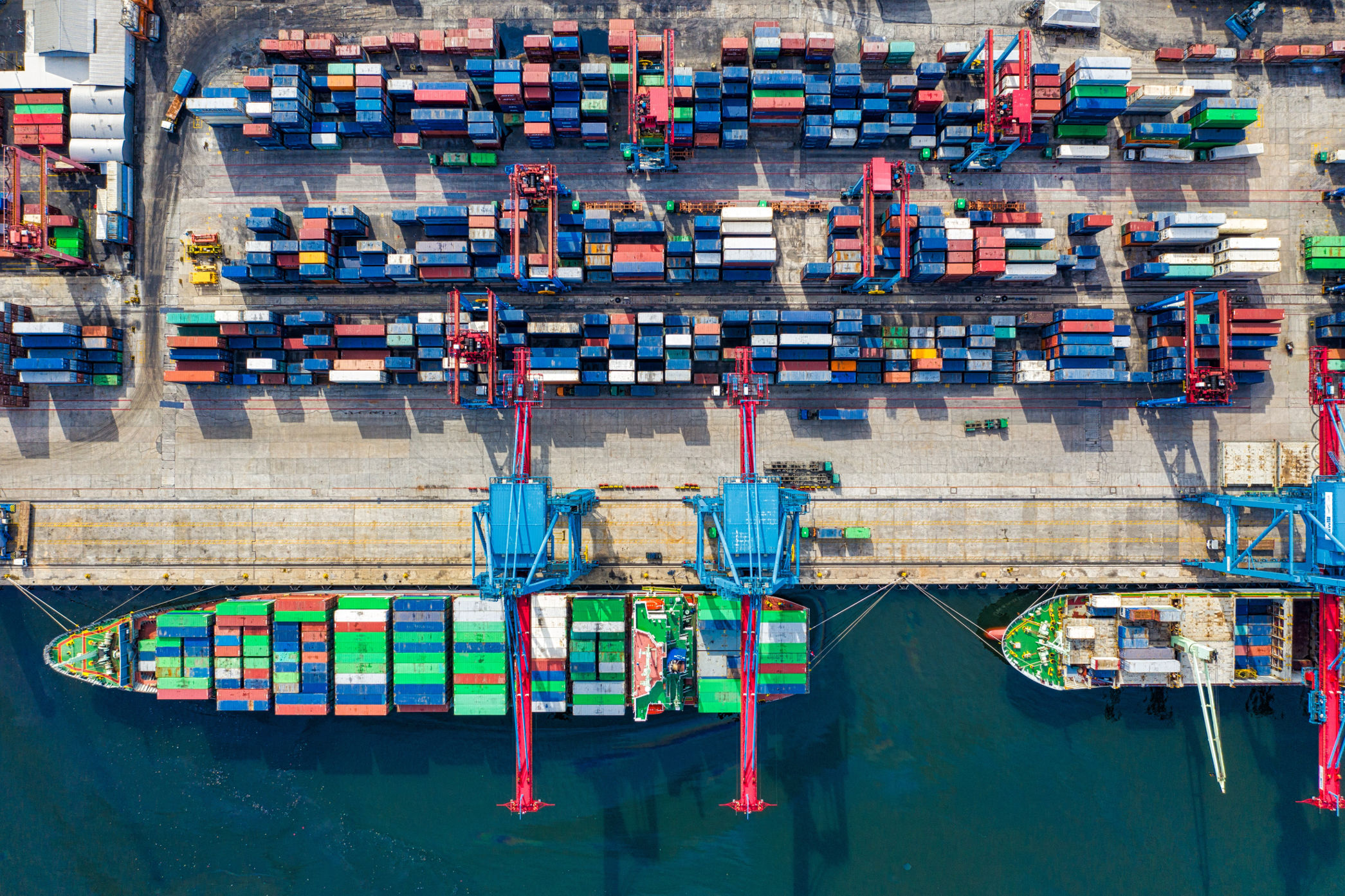
On the surface, supply chain and procurement functions may seem like largely the same thing—both deal with sourcing products and services from outside vendors. But when you look under the hood, there are some key differences between the two that procurement managers should keep in mind.
What’s included in a supply chain?
The term “supply chain” refers to the series of activities involved in the production and distribution of goods or services to customers. The supply chain encompasses everything from sourcing raw materials to delivering finished products to the end consumer. It’s a complex and interconnected system involving various parties, including suppliers, manufacturers, distributors, and retailers.
{{cta1}}
The supply chain consists of several components, each of which plays a crucial role in the overall process. These components include:
Sourcing
Sourcing involves identifying and acquiring raw materials, components, or services from suppliers. Companies need to develop strong relationships with suppliers and choose those that offer the best quality, price, and delivery terms.
Manufacturing
The manufacturing process entails transforming raw materials into finished products. Companies must focus on producing goods efficiently, maintaining high-quality standards, and reducing waste.
Distribution
Distribution involves delivering finished products to customers through various channels, such as warehouses, distribution centers, and retail outlets. Effective distribution strategies can help companies minimize costs, optimize inventory levels, and ensure timely delivery.
Logistics
Logistics management deals with the transportation and storage of goods throughout the supply chain. Efficient logistics can reduce transportation costs, minimize delays, and ensure that products are available where and when they are needed.
Inventory management
Inventory management involves monitoring and controlling the levels of raw materials, work-in-process, and finished goods to ensure optimal stock levels and minimize costs. For SaaS companies, it can also refer to managing your tech stack with app inventories. Companies must strike a balance between having too much inventory, which can lead to increased carrying costs and obsolescence, and too little inventory, which can result in stockouts and lost sales.
{{cta1}}
The crucial role of supply chain management
Effective supply chain management is critical for any organization, as it directly impacts its bottom line. By streamlining and optimizing supply chain processes, companies can reduce costs, improve efficiency, and enhance customer satisfaction.
Companies that excel in supply chain management can enjoy various benefits, such as improved collaboration between suppliers and partners, reduced lead times and inventory levels, enhanced flexibility and responsiveness to market changes, and better customer service and satisfaction.
Procurement is a subset of the supply chain
Procurement is a subset of the supply chain that deals specifically with the process of acquiring goods and services from external suppliers. Procurement involves activities such as supplier selection, contract negotiation, and order management. The primary goal of procurement is to obtain the necessary products and services at the best possible value while meeting the organization's requirements for quality, quantity, and delivery.
Procurement consists of several interconnected components, each playing a vital role in the overall process. These include:
Supplier selection
This involves identifying, evaluating, and choosing the most suitable suppliers for the organization. Companies must carefully assess potential suppliers based on factors such as price, quality, reliability, and delivery performance.
Contract negotiation
Contract negotiation entails establishing agreements with suppliers that outline pricing, terms, and conditions for the delivery of goods and services. Companies must negotiate contracts that protect their interests while fostering strong relationships with suppliers.
Order management
Order management encompasses the entire purchasing process, from issuing purchase orders to tracking deliveries and processing invoices. Effective order management can help companies reduce costs, improve efficiency, and ensure that goods are delivered on time and in the right quantities.
Supplier relationship management
Supplier relationship management (SRM) involves developing and maintaining strategic relationships with key suppliers to ensure long-term success and continuous improvement. By collaborating closely with suppliers, companies can drive innovation, reduce costs, and enhance overall performance.
Spend analysis
Spend analysis is the process of collecting, analyzing, and reporting on procurement data to identify cost-saving opportunities and inform strategic decision-making. Companies can use spend analysis to uncover inefficiencies, monitor supplier performance, and optimize procurement processes.
The importance of effective procurement management
Effective procurement management is crucial for organizations, as it can lead to significant cost savings and improved operational efficiency. When companies manage their procurement activities strategically, they can enjoy a range of benefits, including cost savings through smart sourcing and bringing suppliers together, better relationships and performance from suppliers, and even value creation.
Supply chain vs procurement: Examining the key differences
While procurement and supply chain management are closely related, they have distinct roles and responsibilities within an organization. The following are some key differences between the two:
Scope
The supply chain is a broader concept that encompasses the entire process of producing and delivering goods or services. In contrast, procurement focuses specifically on the purchasing activities within the supply chain.
Objectives
Supply chain management aims to optimize the entire production and distribution process, while procurement's primary goal is to acquire the necessary products and services at the best value.
Stakeholders
The supply chain involves various stakeholders, including suppliers, manufacturers, distributors, and retailers. Procurement primarily deals with suppliers and internal stakeholders within the organization.
Harnessing synergies between supply chain and procurement
To achieve optimal results, organizations should recognize the interdependence between supply chain and procurement management. By closely aligning these two functions, companies can unlock significant benefits, such as:
- Improved end-to-end visibility: When procurement and supply chain teams collaborate, they can gain a better understanding of the entire production and distribution process. This increased visibility allows organizations to identify opportunities for improvement and make more informed decisions.
- Enhanced supplier relationships: Collaboration between procurement and supply chain teams can lead to stronger relationships with suppliers. This, in turn, can result in better pricing, improved service levels, and increased responsiveness to changes in demand.
- Streamlined processes: When procurement and supply chain teams collaborate, they can identify and eliminate inefficiencies in the sourcing, manufacturing, and distribution processes. This can lead to reduced costs, faster delivery times, and improved overall performance.
- Increased agility: A well-integrated procurement and supply chain function can help organizations respond more effectively to market fluctuations, changing customer requirements, and potential disruptions. This increased agility can provide a competitive advantage and promote long-term success.
The role of technology in supply chain and procurement integration
The integration of supply chain and procurement is facilitated by advancements in technology. Modern software solutions can improve communication between teams, increase visibility across the supply chain, and automate time-consuming tasks. Some examples of technology that can support integration include:
Enterprise resource planning (ERP) systems
These software solutions can help organizations manage various business processes, including procurement and supply chain management, by providing a centralized platform for data collection, analysis, and reporting.
E-procurement platforms
E-procurement tools streamline the purchasing process by automating tasks such as supplier selection, order placement, and invoice processing. By using these platforms, organizations can reduce manual efforts, minimize errors, and enhance overall efficiency.
Supply chain management (SCM) software
These applications focus on managing and optimizing supply chain processes, such as inventory management, demand planning, and logistics. SCM software can help organizations improve visibility, reduce lead times, and optimize resource utilization.
Data analytics and business intelligence tools
Data analytics and business intelligence tools enable organizations to analyze procurement and supply chain data, uncover insights, and make informed decisions. By leveraging data analytics, companies can build business intellligence reports and identify trends, opportunities, and potential issues, enabling them to make proactive decisions and drive continuous improvement.
Best practices for integrating supply chain and procurement
To maximize the benefits of an integrated supply chain and procurement approach, organizations should consider implementing the following best practices:
- Develop a cross-functional team: Form a team that comprises representatives from both procurement and supply chain functions. This team can work together to identify opportunities for improvement, streamline processes, and align strategies.
- Establish common goals and key performance indicators (KPIs): Ensure that procurement and supply chain teams are working towards shared objectives by defining common goals and KPIs. This can promote collaboration and help track the progress of integration efforts.
- Foster a culture of collaboration: Encourage open communication and information sharing between procurement and supply chain teams. This can help break down silos and create a more collaborative working environment.
- Invest in training and development programs: Enhance the skills and knowledge of procurement and supply chain professionals by providing training and development opportunities. This can enable them to work together more effectively and contribute to the success of the integrated function.
- Continuously monitor and improve performance: Regularly review processes and make adjustments as needed to ensure ongoing improvement and alignment with organizational goals. By adopting a continuous improvement mindset, organizations can stay ahead of the competition and adapt to changing market conditions.
Understanding the differences between procurement and the larger supply chain is crucial for procurement managers seeking to optimize their organization's operations. By recognizing the distinct roles of each function, as well as their interdependence, organizations can unlock significant benefits, including improved efficiency, cost savings, and increased agility.
By implementing these insights and strategies, procurement managers can better position their organizations for long-term success in an increasingly competitive and complex business landscape. With a well-integrated supply chain and procurement function, companies can not only optimize their operations but also become more resilient, agile, and innovative.
{{cta1}}